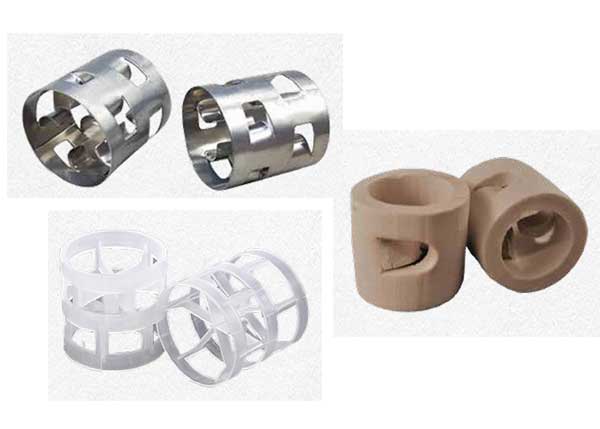
What are Pall Rings?
Pall rings are the most basic, most common type of tower packing. This ring is a versatile and very affordable option for distillation, absorption and stripping processes in various industries. They are used in high-volume and high-temperature processes also. The interior and exterior surfaces of the pall ring efficiently distribute fluids and gases. They are very popular in the industry for their good capacity at the low-pressure drop. Pall rings can be made from metal, plastic, or ceramic materials, all of which have excellent corrosion resistance for use in corrosive environments.
Features
- 20–40% packing volume saving
- 20% higher mass transfer efficiency
- 50% pressure drop reduction under the same handling capacity
- 50% increased handling capacity than Raschig ring under the same pressure drop
Material
- Stainless Steel 316/L, 304/L, 410, Inconel, Monel, Hastelloy, etc.
- Plastic - PP, RPP, CPVC, PVDF and PVC
- Ceramic
Applications :
- Suitable for high-temperature processes
- Higher loading capacity and throughput
- Low-pressure drop
- Higher mass transfer efficiency
- Good fouling resistance
- Plastic Pall Ring: Medium and low temperature distillation, absorption and washing towers in chemical, petroleum, chlor-alkali, coal gas and environmental protection industries
- Ceramic Pall Ring: Contacting packing for carbon dioxide degassing tower, acid fog purifying tower, ozone contact reaction tower and other reaction towers
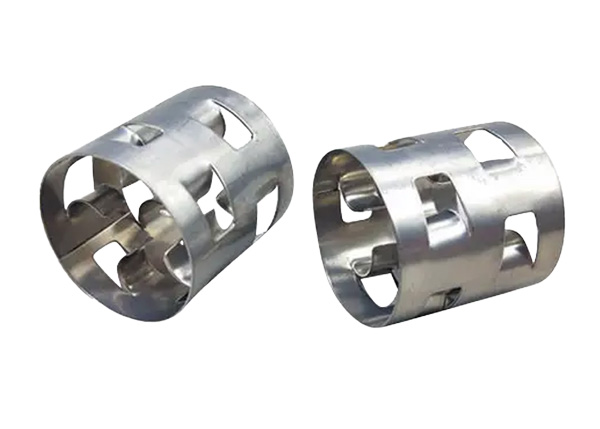
Metal Pall Rings
Metal Pall Rings are a type of random packing used in chemical processing towers, typically for distillation, absorption, and stripping processes. They are made of metal, often stainless steel or other corrosion-resistant alloys, and feature a unique design with cylindrical walls and inward-bent protrusions. These protrusions or "fingers" provide increased surface area and promote efficient gas-liquid contact, enhancing mass transfer and separation processes within the tower. Metal Pall Rings are favored for their high mechanical strength, resistance to fouling, and longevity in harsh operating conditions. They are widely used in various industries such as petrochemical, pharmaceutical, and environmental engineering.
Features of Metal Pall Rings
- High loading capacity and throughput
- Effective liquid and gas separation capabilities with high efficiency
- Resistance to corrosion and rust
- Low pressure drop
- Temperature resistance
- High mechanical capacity with a reduced likelihood of breakage
- Different sizes and specialized dimensions can be tailored to specific requirements
Technical Parameters of Metal Pall Ring | ||||||
---|---|---|---|---|---|---|
Item | Ring Diameter (mm) |
Diameter × Height × Thickness (mm) |
Surface Area (m2/m3) |
Void Fraction | Bulk Density (kg/m3 |
Packing Factor (m-1) |
APM-01 |
16 |
16 × 16 × 0.4 |
239 |
92.8% |
143000 |
299 |
APM-02 |
25 |
25 × 25 × 0.6 |
219 |
93.4% |
55900 |
269 |
APM-03 |
38 |
38 × 38 × 0.8 |
129 |
94.4% |
13000 |
153 |
APM-04 |
50 |
50 × 50 × 1.0 |
112 |
94.9% |
6500 |
131 |
APM-05 |
76 |
76 × 76 × 1.2 |
72 |
95.1% |
1830 |
84 |
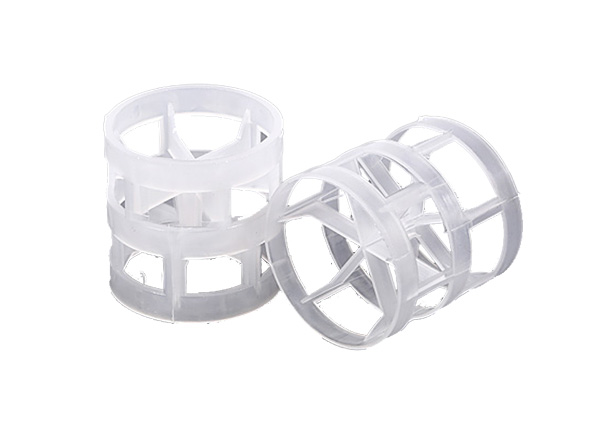
Plastic Pall Rings
Plastic pall rings are increasingly favored in gas and liquid separator applications. They boast exceptional chemical resistance, temperature stability, and mechanical strength. Variants include Polypropylene (PP), Polyethylene (PE), RPP, PVDF, PVC, and CPVC pall rings. Like metal Pall Rings, they feature a cylindrical shape with inward-bent protrusions or "fingers" that provide a large surface area for gas-liquid contact. Plastic Pall Rings offer benefits such as corrosion resistance, lightweight design, and cost-effectiveness compared to metal alternatives. They are commonly utilized in industries where corrosion resistance and durability are crucial, including wastewater treatment, air pollution control, and chemical processing.
Features of Plastic Pall Rings
- High mechanical strength
- Exceptional operational versatility
- High separation efficiency
- High mechanical strength
- Diverse internal configurations adaptable to various applications
Technical Parameters of Plastic Pall Ring | ||||||
---|---|---|---|---|---|---|
Item | Ring Diameter (mm) |
Diameter × Height × Thickness (mm) |
Surface Area (m2/m3) |
Void Fraction | Bulk Density (kg/m3) |
Packing Factor (m-1) |
APP-01 |
16 |
16 × 16 × 1.1 |
188 |
91% |
112000 |
249 |
APP-02 |
25 |
25 × 25 × 1.2 |
175 |
90% |
53500 |
239 |
APP-03 |
38 |
38 × 38 × 1.4 |
115 |
89% |
15800 |
220 |
APP-04 |
50 |
50 × 50 × 1.5 |
112 |
90% |
6500 |
154 |
APP-05 |
76 |
76 × 76 × 2.6 |
73 |
92% |
1930 |
94 |
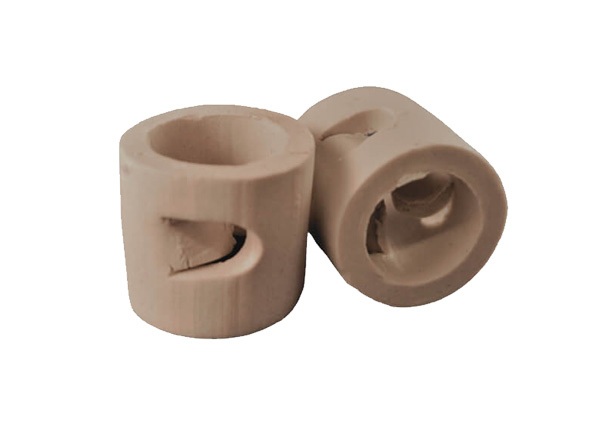
Ceramic Pall Rings
Ceramic pall rings represent a classical form of random packing, derived from the Raschig ring design. Typically, they feature two layers of windows along the cylindrical wall, with each layer containing five inward-bending ligules, akin to metallic and plastic pall rings. However, the arrangement and number of ligules may vary depending on the height and diameter specifications. Typically, around 30% of the cylinder wall's total area is dedicated to openings. This configuration facilitates unhindered flow of vapor and liquid through the windows, maximizing utilization of the ring's inner surface to enhance vapor and liquid distribution. Consequently, this design can elevate separation efficiency.
Features of Ceramic Pall Rings
- High chemical stability
- High mechanical strength
- Resistance to acids, alkalis, salts, and diverse organic solvents
- Outstanding heat endurance
- Sizes and window configurations are customizable to suit varying applications and specifications
Technical Parameters of Ceramic Pall Ring | ||||||
---|---|---|---|---|---|---|
Item | Diameter × Height × Thickness (mm) |
Surface Area (m2/m3) |
Void Fraction | Bulk Quantity (pcs/m3 |
Bulk Density (kg/m3) |
Packing Factor (m-1) |
APC-01 |
25 × 25 × 3 |
238 |
73% |
54000 |
520 |
565 |
APC-02 |
38 × 38 × 4 |
197 |
75% |
13400 |
570 |
365 |
APC-03 |
50 × 50 × 5 |
154 |
78% |
6800 |
550 |
252 |
APC-04 |
80 × 80 × 8 |
116 |
80% |
1950 |
520 |
146 |
Global Export of Metal Pall Rings
Ambani Metals is a trusted global manufacturer and exporter of Metal Pall Rings, engineered for superior mass transfer efficiency, low pressure drop, and robust mechanical strength in packed columns. Designed with open windows and internal fingers, Pall Rings offer enhanced gas-liquid contact and reduced channeling, making them ideal for distillation, absorption, stripping, and scrubbing applications across a range of process industries.
Manufactured using high-quality metals such as Stainless Steel 304/316L, Carbon Steel, Hastelloy, Inconel, Monel, Titanium, and more, our Pall Rings ensure long-lasting durability and chemical resistance in even the harshest process conditions.
Ambani Metals exports Metal Pall Rings to clients across 40+ countries, delivering precision-made internals with full QA/QC documentation, export-compliant packaging, and custom sizing as per international standards.
- Middle East: Bahrain, Egypt, Israel, Jordan, Kuwait, Lebanon, Oman, Qatar, Saudi Arabia, and the United Arab Emirates
- Africa: Morocco, Tunisia, Ghana, Nigeria, Senegal, Kenya, Mauritius, Rwanda, Tanzania, Uganda, Zambia, Botswana, Eswatini, Lesotho, Namibia, and South Africa
- Europe: Germany, United Kingdom, France, Italy, Netherlands, Spain, Belgium, Poland, Czech Republic, Sweden, Denmark, Finland, Portugal, Hungary, Slovakia, Slovenia, Romania, and Austria
- Asia: Japan, South Korea, Singapore, Malaysia, Vietnam, Indonesia, Thailand, Philippines, Bangladesh, Sri Lanka, and Nepal
- Pan-Pacific Countries: United States, Canada, Mexico, Brazil, Chile, Colombia, Peru, Panama, Australia, and New Zealand
Why Choose Ambani Metals?
- High-performance packing for reliable and efficient separation
- Available in multiple alloys and sizes to suit all column designs
- Fast turnaround and global delivery with export documentation
- In-house R&D, engineering, and QA/QC support
- Competitive pricing with bulk export capacity
When your column demands high efficiency and rugged performance, Ambani Metals’ Metal Pall Rings deliver the perfect balance of design, durability, and cost-effectiveness—trusted globally by industry leaders.