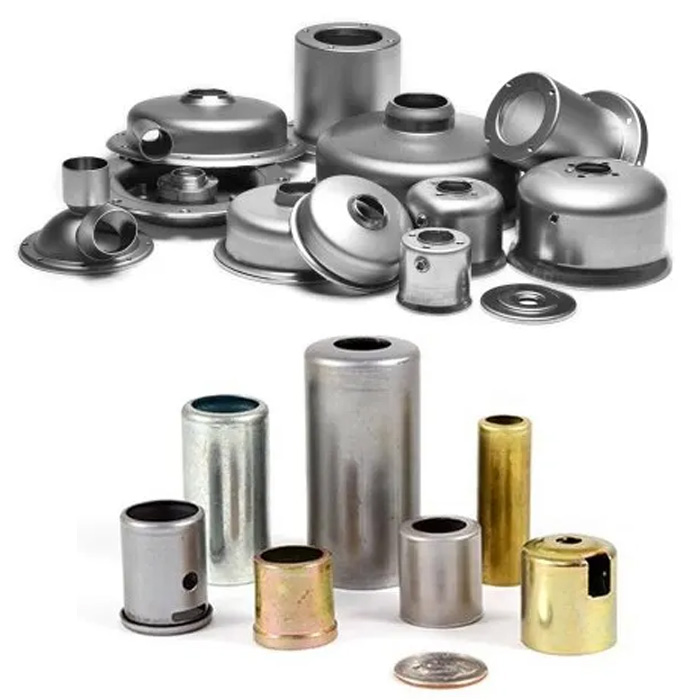
Ambani Metals produce high volume deep drawn components for a variety of industries, including automotive components, aerospace components, and more. Our deep draw part capabilities include in-house tooling combined with design and engineering support for diverse applications including cans, caps, cases, connectors, cups, eyelets, ferrules, housings, shells and more.
The deep-drawn process is a widely used manufacturing process that is extremely popular amongst companies due to its ability to produce high-precision metal parts in large volumes. This process involves the use of a die that shapes the metal parts into specific designs that are highly accurate and uniform. The process begins with pre-shaped metals such as blanks, discs or tubes which are then placed into the die and pressed by a press ram. As the pressing force increases, the shape of the metal part is further formed until it reaches its desired form.
The deep-drawn process offers numerous benefits for manufacturing companies, including cost savings from production speed and accuracy. Its ability to produce high-precision components at large volumes means less scrap and fewer wasted materials, resulting in greater efficiency when producing complex geometries.
What is the Deep Draw Stamping Process?
Deep drawing is the perfect process for high-volume manufacturing. It enables companies to achieve components with exceptional repeatability and accuracy at a lower cost compared to other processes – such as turned and machined components.
How this deep draw stamping process works
Starting with a metal blank, the disc of metal cut from a larger sheet is pushed into a cavity around a die, which begins the deep drawn process of drawing the blank into the desired shape. This is completed in gradual steps to ensure an even distribution of the metal across the final shape, which is important for preserving the integrity and strength of the finalised deep-drawn component.
The raw material used is in strip form. The first operation at the press cuts a flat blank from the strip of raw material. The blank is then carried by transfer fingers to the next operation where a cup is drawn. The cup is then transferred to the next station where the metal is drawn in a percentage allowed.
Virtually all manufacturing industries have the potential to benefit from deep-drawn metals for the manufacturing process. This technique is often used for manufacturing small parts such as electronics relays, solenoids and assembly housing.
However, products of all shapes and sizes can be economically created through this deep drawing process. Everything from aluminium cans to cookware and kitchen sinks can be customized and created through this process.
The deep drawing process is especially beneficial when producing high volumes of products, as unit cost decreases as the unit count increases.
This is because once the tooling and dies have been created, the process can continue without much downtime or upkeep. However, even at small volumes, deep drawing can be more cost-effective than similar manufacturing processes, such as progressive die stamping.
Another benefit to deep drawing is that it is ideal for products that require substantial strength and minimal weight. It is also recommended for products whose geometries are unachievable through other methods.
While cylindrical objects such as aluminum cans or metal diaphragms are usually the most popular use of this method, squares, rectangles and more complex geometries are still easily and efficiently created through the deep drawing process.
Deep Drawn Parts :
- Deep Drawn Cans
- Deep Drawn Caps
- Deep Drawn Eyelets
- Enclosures
- Deep Drawn Cups
- Deep Drawn Covers
- Deep Drawn Fasteners
- Deep Drawn Ferrules
- Deep Drawn Pins
- Deep Drawn Shells
- Deep Drawn Housings
- Deep Drawn Terminals
- Deep Drawn Nozzles
- Deep Drawn Tubes
- Deep Drawn Cases
The Benefits of Deep Draw Stamping
- Speed - No other process can match the speed of a punch press moving up and down. It's usually the most efficient method if you need a large quantity of parts making.
- Eliminates assembly steps - Deep drawing produces shapes with closed ends. That avoids the need to cut and weld multiple pieces.
- Seamless - A deep drawn can or tube shape has no joins. That makes deep drawing an ideal process for anything that needs to be water or gas-tight.
- High accuracy - Parts coming off a forming press are extremely repeatable. Assuming the tooling was made correctly, they'll also conform very closely to the drawing.
- Produces complex geometries - We've talked here about simple shapes like cans and sinks, but deep drawing can create more complex forms. How about the oil pan for an engine or complex filter housings?
- Produces very strong parts - Many metals work-harden as they deform. Essentially, their crystal structure allows a certain amount of movement but beyond that it becomes locked. Deep drawing subjects metal to a lot of deformation, so can result in very hard finished parts.
Uses of Deep Drawn Stamping
Deep drawing may be a viable solution for any manufacturing process that includes one or more of the following :
- Seamless parts: deep drawn metal parts are created from a single sheet of metal
- Rapid cycle times: large quantities of products are easily manufactured through the deep draw process
- Complex axisymmetric geometries: deep drawing delivers exceptional detail and accuracy
- Reduced technical labour: precision deep drawing can deliver similar results as technical labour in quicker time frames
Applications of Deep Drawn Parts & Components:
- Aerospace
- Automobile
- Bracket
- Distillery
- Electrical Appliance Hardware
- Electronic Hardware
- Frame Structures
- Heaters
- Metal Eyelet
- Motors
- Pumps
- Valves
Global Export of Deep Drawn Metal Stamping
Ambani Metals is a trusted manufacturer and global exporter of Deep Drawn Metal Stamping Parts, engineered for seamless, strong, and accurate metal enclosures, cans, caps, shells, and housings used in automotive, electrical, electronics, medical, HVAC, defense, and industrial applications.
Using advanced hydraulic and mechanical deep drawing presses, our facility produces components with consistent wall thickness, tight tolerances, and superior structural integrity, even in complex or asymmetrical shapes, without joints or welds.
Key Capabilities:
- Drawing depth: Up to 200 mm | Wall thickness: 0.3 mm – 5 mm
- Tolerances: Up to ±0.05 mm
- Shapes: Cylindrical, rectangular, square, stepped, flanged, bellows, and custom geometries
- Materials: Stainless Steel (304, 316), Brass, Copper, Aluminum, Cold-Rolled Steel, Nickel Alloys
- Surface Finishes: Electropolishing, Anodizing, Passivation, Powder Coating, Plating
Ambani Metals exports deep drawn parts to clients across the globe who demand leak-free performance, seamless construction, and mass-production consistency.
- Middle East: Bahrain, Egypt, Israel, Jordan, Kuwait, Lebanon, Oman, Qatar, Saudi Arabia, and the United Arab Emirates
- Africa: Morocco, Tunisia, Ghana, Nigeria, Senegal, Kenya, Mauritius, Rwanda, Tanzania, Uganda, Zambia, Botswana, Eswatini, Lesotho, Namibia, and South Africa
- Europe: Germany, United Kingdom, France, Italy, Netherlands, Spain, Belgium, Poland, Czech Republic, Sweden, Denmark, Finland, Portugal, Hungary, Slovakia, Slovenia, Romania, and Austria
- Asia: Japan, South Korea, Singapore, Malaysia, Vietnam, Indonesia, Thailand, Philippines, Bangladesh, Sri Lanka, and Nepal
- Pan-Pacific Countries: United States, Canada, Mexico, Brazil, Chile, Colombia, Peru, Panama, Australia, and New Zealand
From tiny caps to deep metal shells, Ambani Metals’ Deep Drawn Parts provide leak-proof, high-performance solutions trusted by global OEMs across high-precision industries.