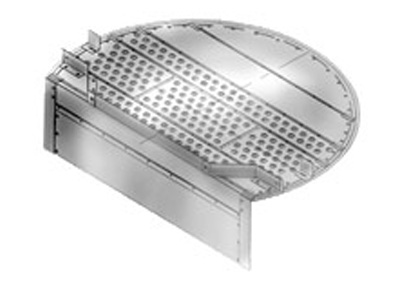
A sieve tray is a perforated plate tray, with holes punched into the surface area of the deck plate. The holes range from 3/16 to 1 inch. Sieve trays are suitable for applications where turn down ratio is not critical. The vapor passes through the holes and keeps the liquid on the tray deck. These perforated sieve trays are designed to handle high loads and are suitable for all applications where turndown is limited to 2:1 with a medium fouling tendency. With our in-house manufacturing facility and experienced production team, we can assure you that the sieve trays are manufactured to achieve optimum performance.
Features
- Cost effective solution
- For different capacity and pressure drop requirement
- Robust construction
- Fouling resistance
Material of Construction
- SS 304/L, SS 316/L, 904L, 254SMO, Duplex, Super Duplex, Titanium, Hastelloy, Monel, Inconel, Copper or any metal/alloy as per customer request
Key Characteristics
- Low cost. Not flexible for wide range of turndown ratio. High capacity and efficiency, low pressure drop, ease of cleaning, and low capital cost.
Available Size
- Sieve Trays are available up to 6m diameter
Global Export of Sieve Trays
Ambani Metals is a premier manufacturer and global exporter of sieve trays, engineered for reliable and cost-efficient vapor-liquid contact in distillation and absorption columns. Known for their simplicity, low maintenance, and excellent hydraulic performance, our sieve trays are trusted by process industries around the world for both new installations and column revamp projects.
Fabricated from high-grade materials like Stainless Steel 304/316, Duplex Steel, Inconel, Hastelloy, and other exotic alloys, our sieve trays are built to perform under varied process conditions, from high-throughput petrochemical towers to precision separation systems in the pharmaceutical sector.
With precision engineering, global packaging standards, and timely dispatch, Ambani Metals exports sieve trays to more than 40 countries, serving global EPC contractors, OEMs, and end-users.
- Middle East: Bahrain, Egypt, Israel, Jordan, Kuwait, Lebanon, Oman, Qatar, Saudi Arabia, and the United Arab Emirates
- Africa: Morocco, Tunisia, Ghana, Nigeria, Senegal, Kenya, Mauritius, Rwanda, Tanzania, Uganda, Zambia, Botswana, Eswatini, Lesotho, Namibia, and South Africa
- Europe: Germany, United Kingdom, France, Italy, Netherlands, Spain, Belgium, Poland, Czech Republic, Sweden, Denmark, Finland, Portugal, Hungary, Slovakia, Slovenia, Romania, and Austria
- Asia: Japan, South Korea, Singapore, Malaysia, Vietnam, Indonesia, Thailand, Philippines, Bangladesh, Sri Lanka, and Nepal
- Pan-Pacific Countries: United States, Canada, Mexico, Brazil, Chile, Colombia, Peru, Panama, Australia, and New Zealand
Why Choose Ambani Metals for Sieve Trays?
- International manufacturing and design standards (TEMA, ASME)
- Full customization based on column diameter and process load
- Surface finishes for anti-fouling and corrosion resistance
- Global technical support and fast-track delivery
- Export-compliant documentation and packaging
Whether for turnkey plant supply or critical revamp work, Ambani Metals is your trusted partner for sieve trays that combine engineering precision with long-term reliability, shipped globally with confidence.
FAQs
A sieve tray is a type of tray used in distillation columns to facilitate the separation of components in a mixture based on their volatility.
Sieve trays work by allowing vapor to pass through while holding back liquid. They consist of a perforated plate with holes (sieves) through which vapor rises, contacting liquid on the tray. The liquid flows through the perforations, while the vapor continues upward, promoting separation.
Sieve trays are typically made from materials like stainless steel, carbon steel, or other corrosion-resistant alloys. The choice of material depends on factors such as the corrosiveness of the substances being processed and the operating conditions of the distillation column.
Sieve trays offer several advantages, including high efficiency in separating liquid and vapor phases, relatively low pressure drop compared to other tray types, and good resistance to fouling.
Sieve trays are generally simpler in design compared to bubble cap trays. They have higher capacity and efficiency but may be more prone to liquid entrainment. Bubble cap trays, on the other hand, provide better liquid/vapor contact but have higher pressure drops and are more complex to manufacture and maintain.
In distillation, sieve trays play a crucial role in promoting the separation of components with different volatilities. They provide a surface for liquid-vapor contact, allowing the more volatile components to vaporize and rise while the less volatile ones remain in the liquid phase.